How Is Toughened Glass Made?
Toughened glass is made when annealed float glass is heated to 620˚C. The point just before the glass softens.
The glass is then rapidly cooled with cold-blown air.
This process causes the outer surfaces of the glass to harden before the centre of the glass and this creates a compressive stress. The interior of the glass is held under tensile stress by the compressive stress of the outer layers.
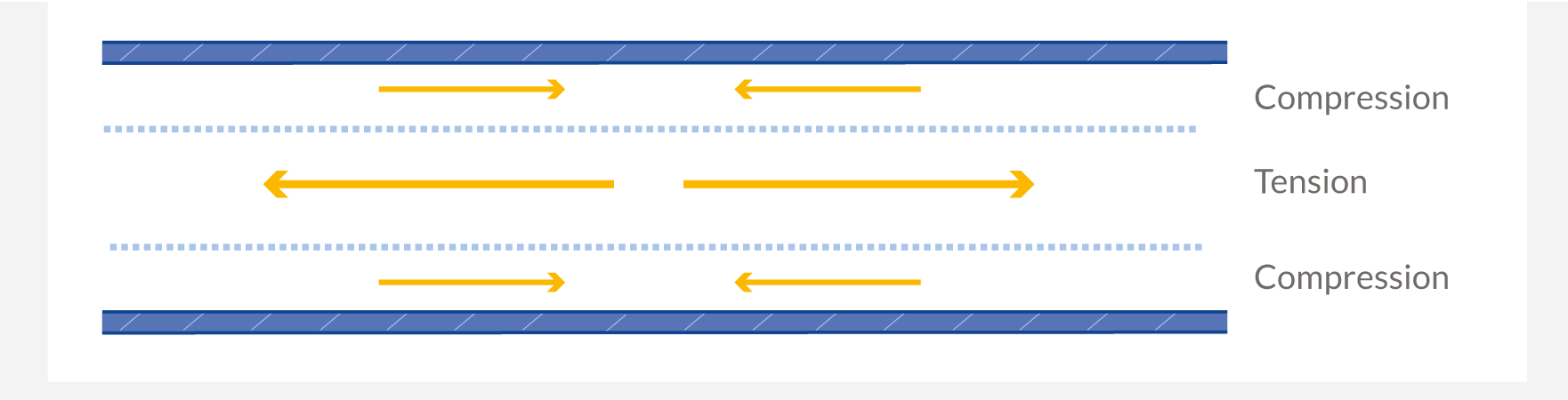
The stress and tension are what create the enhanced strength of the glass. It also makes the glass break in an explosive manner which produces small cube-like fragments of shattered glass.
The glass must be cut to size before heating as any cutting or grinding after being tempered will cause the glass to break.
Toughened Glass Uses
Toughened glass is used for safety where there is any danger of injury from impact and shards of broken glass. Although in some instances laminated glass is also used for safety, toughened glass is more economical and used more widely.
Because toughened glass has a high breaking point, and it also breaks into granular pieces, it's used in car side windows and rear windows. Windscreens only use laminated glass to protect the eyes or face from small pieces of glass should the screen break at speed.
In the home, toughened glass must be used in what is considered a 'critical location' which includes windows up to 800mm and doors up to 1500mm from floor level. Read more here...
Toughened glass is also used for:
- Low-level glazing in critical locations
- Shower screens and bathrooms
- Splashbacks and shelving
- Worktops
- Tabletops and shelves
- Fireplaces
- Balcony doors
- Swimming pools
- Shop fronts (where security is not an issue)
- Mobile phone screen protectors
Toughened Glass Disadvantages and Limitations
The main disadvantage of toughened glass is that it doesn't offer any security protection like laminated glass as it does shatter into small pieces with very hard impact. So, where security is also a risk, such as back doors or secluded windows, laminated glass is the better choice.
Toughened glass is also weakest on the edges where the tensile stress is the greatest. This means it can't be cut or ground after being tempered. The glass must be cut to size and finished before being heat treated.
Another issue to be aware of is a natural and inherent flaw in Nickel Sulphide (NiS) inclusions which can be found in standard glass. The naturally occurring contaminant cannot cool as quickly as the glass after heating and this causes it to have an internal weakness and there is a low risk the glass can fracture.
Toughened glass can be heat soaked during manufacturing where the glass is heated again to 250 & 290°C. This will accelerate the flaws in the glass so they are revealed and fail at this stage and not after fitting. Please note that the toughened glass used in Everest glazing has not undergone the heat-soaking process during manufacturing.
Heat soaking carries a European standard of EN 14179 which defines the appropriate test method.
Annealed glass or even heat-treated glass does not have the same weakness.
Heat-strengthened glass doesn’t have the same weakness to NiS as toughened glass and is sometimes used as an alternative. However, heat-strengthened glass has a break pattern like annealed glass and does not meet safety standards for critical locations, unless it's been laminated.